

It was money that could be better spent on marketing the new models or adding showroom space. To handle the burgeoning pile of new parts. This was space the distribution center could have used to speed up the unloading of parts arriving from the feeder facilities in California and Kentucky.Īs Toyota sold more cars and models in the U.S., the problems would get worse - and more expensive - if dealers and distribution centers had to knock out walls and add staff And the parts distribution center needed dock space equivalent to the two trailers to stage the shipment. The dealer needed manpower and space to unload and stock the huge shipments. A big dealership in El Monte, CA, required two 48-foot trailers to deliver its weekly order. The traditional system was inefficient for dealers, too. The trick was to get the critical order volume down and the stock order volume up because the big productivity gains came from picking stock orders of standard replacement parts like spark plugs, filters, hoods, bumpers, etc. “We were making twice as many moves through the warehouse for each dealer.” Critical order volume climbed to as much as 45% of the daily order volume. “Basically what we did in any warehouse in the country was go through once to pick the stock order then go through later in the day to pick the critical orders,” explained Gallagher. The system also hurt productivity at the parts centers as dealers would place daily “critical” parts orders - parts that had run out – in addition to their weekly stock orders. In turn, the automaker’s network of 11 parts distribution centers needed large inventories to supply dealers. Like any conventional distribution system with its low-frequency, large-lot replenishment cycles, this system baked in a lot of waste.įor instance, since dealers couldn’t accurately predict what parts customers would need the following week, they kept large inventories on hand to assure a consistent supply in between weekly deliveries. In turn, Gallagher’s parts distribution center received a large weekly shipment of North American-made parts from a feeder warehouse in Kentucky and a large weekly shipment of Japanese-made parts from a feeder warehouse in California. “We used to deliver one large stock order to our dealers every week,” recalled Bob Gallagher, manager of the Toyota parts distribution center in Mansfield, MA. 36 warehouse associates, 5 admin./support associates, 1 manager and 7 leaders (operations/logistics/customer service).Toyota’s Boston Parts Distribution Center at a Glance These aren’t characteristics normally attributed to lean paragon Toyota, but they once accurately described the automaker’s service parts distribution system.
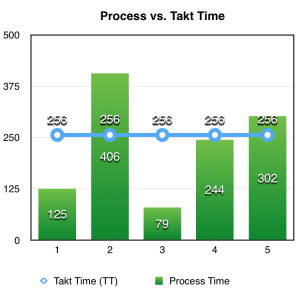
Large inventories to cover fluctuations in demand.
